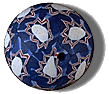 |

Home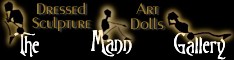

What is Polymer Clay?
Polymer clay is just that, a clay created of polymers or plastics. It is
not technically "clay", that is it is not naturally occurring
in nature, so some prefer use of the term modeling material. In addition
to plasticizer, you'll find resins, gels, fillers and colorants on the
list of ingredients. All polymer clays share the same essential ingredients
but of differing proportions. So Sculpey, Promat, Fimo, Cernit, etc. are
all members of the same family of clays but slightly different in terms
of workability, conditioning, etc. from each other.
Polyform Products clay share the same easy conditioning properties; they
are also the most like natural clay in terms of use and workability. Cernit
is the next easiest to condition, then Fimo, which is the most difficult
to prepare. Thoroughly conditioning polymer clay is of utmost importance;
make sure your clay is soft and pliable (no crumbling and cracking) prior
to use.
In terms of strength, Promat is the most flexible in thin areas, then Cernit,
then Fimo, then Sculpey III. Super Elasticlay is the strongest of all the
polymers, being rubbery and stretchy after curing.
When making figurines or items with parts which are added to parts, simply
press the uncured pieces together and they'll stick. For additional security,
you might insert a piece of wire or a toothpick.
In terms of appearance after curing, Fimo, Cernit, and Promat have a dull
sheen and some think have a more "plastic" appearance. Sculpey,
Promat, Super Sculpey, Sculpey III retain a bisque type finish. They most
resemble natural clay in this regard.
All polymer clays can be painted after curing. Acrylic paint is the recommended
medium. Certain oils can chemically react with the plasticizer in the clay.
Should a reaction take place, the polymer clay becomes sticky and melts.
This does not occur immediately but within a week or so.
Polymer clay can be glazed to impart a sheen. Use water based glazes like
Sculpey Gloss glaze, which is bottled and applied with a brush. You can
also use spray glaze like Carnival Arts glazes but remember to spray lightly,
do not saturate your piece. If possible, prior to glazing, wet sand your
piece. Under running water first sand with 400 grit then 600 grit wet/dry
sandpaper. This will smooth out surface imperfections and yield the best
glazed finish. After sanding, instead of applying glaze, you could buff
to a high sheen with the use of a bench lathe fitted with a muslin wheel
or buff with a soft cotton cloth for a dull sheen.
While polymer clays can be tooled, detailed and textured prior to curing,
remember, you can carve, sand and drill after curing as well.
They all share the same method of curing which is exposure to low heat
(275 degrees F for Polyform clays), while ceramic clays or clays occurring
in nature require the use of high temperature kilns to cure, polymer clays
need only toaster ovens or the oven in your home to render them permanent.
Polymer clay is NEVER to be placed in a microwave oven. Never. They are
NOT designed to cure in a microwave environment.
Polymer clays are non toxic and perfectly safe when properly used. There
is a saying, "A little common sense goes a long way" and it applies
here, too. Never burn your clay; fumes from burnt clay are toxic and should
be avoided. Invest in an oven thermometer and a timer then use them! Follow
the package instructions to the letter and you'll have no problem. Should
you accidentally burn your clay, do not inhale the fumes; open a window
and leave until the fumes have dissipated, 20 minutes or so. If you elect
to use a convection oven, reduce the temperature 10 to 20 degrees to compensate
for the accelerated cooking.
Don't use polymer clay to make food storing or holding items. It's a non
toxic material but you still don't want to ingest it. Decorative use only,
please. This leaves, cookie molds, cups, glasses, etc. out of the picture.
Believe me, there are plenty of uses for this marvelous medium that don't
involve direct contact with food.
|